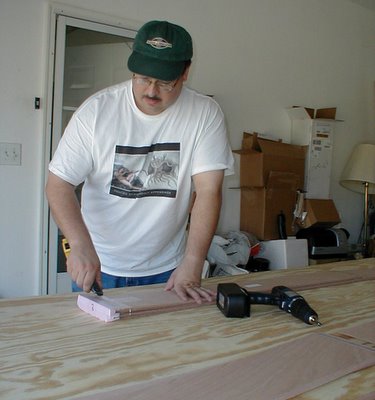
In what may be a sign of how this project goes, I hit a snag right out of the box. Literally. Equipped with a freshly bought piece of plywood, I was ready to set it on some sawhorses for a work bench. Put when I opened the box containing the new sawhorses, I found they were not ready to use, but rather came in many small pieces, with dozens of bolts and screws with which to assemble them. It took nearly an hour and a half to complete that unexpected chore. But then things began in earnest. There was still prep work. I had to unwrap the carefully cut and packaged side planks. The delicate bevel on each piece was wrapped in foam and many layers of tape. Once these eight pieces of lumber were unwrapped, along with the eight rub rail strips, then the epoxy work could begin.

The beveled ends of the rub rails were easily aligned and then epoxied and clamped for overnight curing. The side planks were a little more difficult. They had to be done in pairs, so that each side on the boat would later come into alignment. So the plank from left and right (port and starboard) were stacked up, with plastic sheets separating each layer. The curve of the board had to be carefully measured against a flat reference line for each pair, and then epoxy was applied.

Once aligned and epoxied, the whole stack was clamped down with a board that was screwed into the work table with sheetrock screws. Since I am a little unsure of my technique, I will let the first pair of boards set up overnight and check it tomorrow before I try the other three sets. But at least the project has begun.
Total hours: 2.5