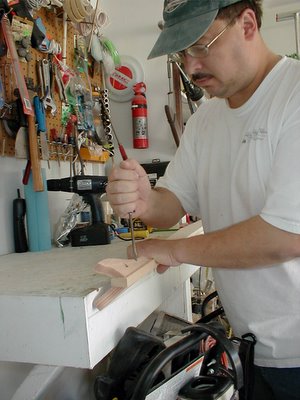
Intending to put a second coat of epoxy on the exterior hull, I instead got sidetracked, and messed around with various boat parts. I first started finishing the daggerboard. Previously,
the handle was laminated on the piece of plywood that makes up the daggerboard. Today, I shaped the board to be more hydrodynamic. The leading edge of the submerged portion was rounded, and the trailing edge was shaped to a fine taper with a belt sander and 100-grit paper. Other edges were rounded with the router and a roundover bit. I switched to the 3/8" roundover bit to shape the handle, which turned out to be good looking with the round contour and all the layers of the laminate showing. I then turned to some finish work on the spars. I attached the gunter yard jaws to this spar. The jaws are shaped plywood that form a fork where the gunter yard rides along the mast. The instructions for this task are a little unclear, with only a warning to put the jaws on the correct end of the yard. However, it is unclear - and not shown in a photo on the page - which direction the jaws angle towards. (Although, after thinking about it, I realize that if they are put on the correct end of the yard, there is only one way they could angle.) For Passagemaker builders, be sure to look ahead to page 85 (the
first page 85; my copy of the instruction book has two) of the instruction book for a photo of the correct orientation. Additionally, the instructions call for the jaws to be preliminarily attached by countersunk screws, but don't specify which of the myriad screws that are included in the sail kit are to be used. Since the yard is rather narrow, I used four of the shortest bronze woodscrews supplied in the sail kit. Later on, the jaws will be permanently epoxied in place along with the screws. Finally, the gunter yard and the mainsail boom were sanded and edges were rounded off with the router to give a finished look. Instructions advise that the spars need not be epoxy coated, but only varnished, which is something I will do later, after the required rigging holes are drilled in the yards.
By the time that was all done, it was far too nice a day to be inside boat building. I took the rest of the afternoon off to enjoy the weather.
Total hours 62.75.